Mitigating DC Connector Risks in PV Systems
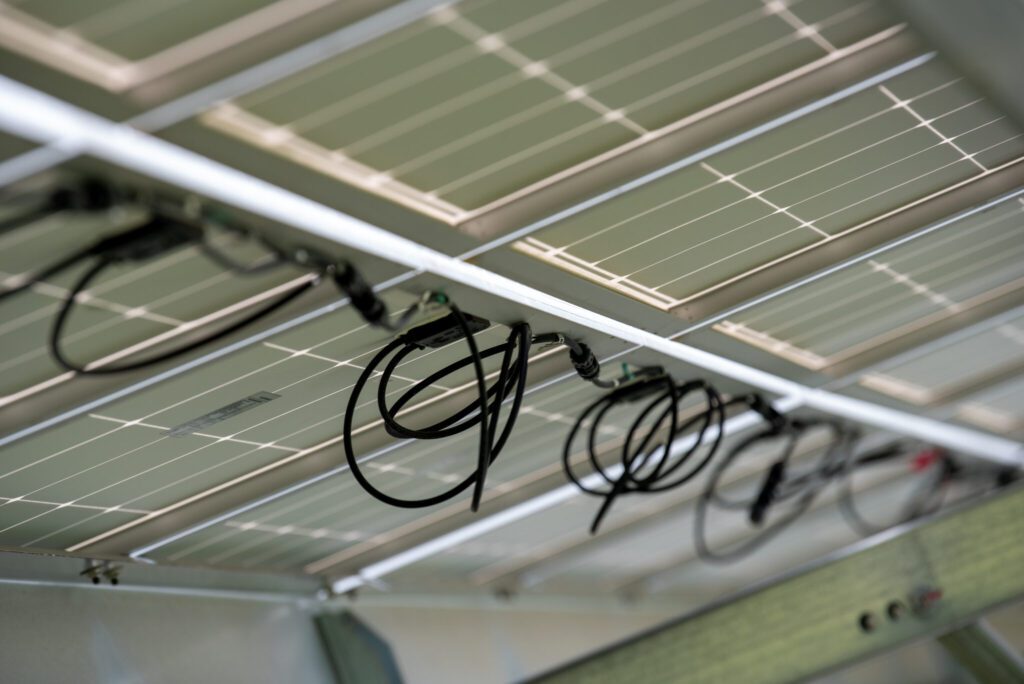
Electrical connection points are essential building blocks for any circuit that often get overlooked. Electrical installations use contactors, quick-connects, and other termination methods to form current-carrying bridges between two or more circuit components. But, just like the overpass by your local highway, these electrical bridges are susceptible to damage, which can have outsized consequences. This blog will focus on the risks associated with DC connectors in PV systems. What issues are prevalent today? How do we solve them? Let’s dive in.
What’s the issue?
Recent studies from reputable research outlets like PVEL and SolarGrade have illuminated the frequency and severity of PV connector problems. The numbers may be surprising.
- PVEL reported that (as of December 2021) there were nearly 3.5 billion PV connections worldwide, and “connectors are a leading cause of fires instigated by PV systems in many global solar markets.”
- SolarGrade assessed the health of hundreds of distributed generation PV systems in the United States. Well over half of their inspections unearthed safety issues “that require urgent correction.” Of the urgent issues they found, 40% were related to field-made or factory-made connectors.
To summarize, PV connectors are ubiquitous in PV systems and aren’t going away soon. Connectors are simultaneously essential to PV system operation and are among the largest risks to its performance. In this case, “connection points” and “potential failure points” are synonymous. The root causes of connector issues, though, are more nuanced.
What’s the context?
Now that we know the scale of the problem, let’s drill down to some of the common causes. Before that, it’s worth mentioning the larger forces at play that impact PV connector issues.
Incomplete Industry Data
Many fires and performance failures go unreported or underreported simply because the data is sensitive. An asset owner may be hesitant to share site details or initiate legal action; an installer may not want to publish information that could expose workmanship issues; and the solar industry at large may prefer to keep data that skews against renewables under wraps. Competing factors often outweigh the incentives to share information on system failures. All of this means that we’re operating with limited information for now and extrapolating from what we know. We can confidently point to a few issues impacting PV connector failure rates.
Lack of Standardization
No universal connector exists, despite the 2020 (and 2023) NEC calling out UL 6703 listing for connectors that are identified for intermatability:
2020 NEC 690.33(C) – Where mating connectors are not of the identical type and brand, they shall be listed and identified for intermatability, as described in the manufacturer’s instructions.
The 2020 NEC clarifies that cross-mating connectors is no longer acceptable. Compliance is possible through the use of connectors of identical type and brand or by using jumpers, which effectively double the number of potential failure points in the system.
The third option for compliance—installing UL 6703-listed connectors—is possible in theory but not in practice. Since field installations must comply with product listing instructions per 2020 (and 2023) NEC 110.3(B), installation manuals supersede UL listings. If you read the assembly instruction documents from the leading connector manufacturers, you will find warnings along the lines of:
“Do not connect the male or female part of [manufacturer] connector with connectors of other manufacturers.”
Thus, according to the connector manufacturers themselves, a universally-compatible connector does not exist. Much like today’s incentive structure can discourage data-sharing about system failures, market forces are at odds with connector standardization. If a manufacturer were to pay to list its product as universally compatible, it would effectively make the product interchangeable with its competitors and could cut into market share.
Workmanship Errors
Of the estimated 3.5 billion PV connections worldwide, it’s safe to assume that human technicians installed the vast majority. Most developers and installers will have rigorous in-house standards and training programs. However, as we’ve learned from our Electrical Testing Standards Guide initiative with Megger, there is limited industry-wide knowledge about PV installation and maintenance best practices. Given that a seemingly small installation error can cascade into much more significant issues, sharing expertise to boost workmanship quality is truly a win-win for everyone involved.
How can I decrease risk?
As the entire PV industry waits for a universal connector, there are a few steps you can follow immediately to decrease the risks associated with connector failure.
Enhance Training Procedures: There is no easy button to resolve workmanship errors, especially when demand is high and the workforce is relatively undersized. However, investing in workforce development and consistently updating your installation and maintenance processes is strongly recommended. Look into third-party training providers if your team is constrained by budgets or personnel. Establish a recurring review of your operations that’s validated with system performance metrics. Gradual steps add up to a significant impact in the long haul, and your customers will be happier.
Optimize Bill of Materials: Avoid the risks associated with connector mismatch by specifying modules and any MLPE with intermatable connectors early in development. Work with your distributor to find the right product mix, and be ready to make adjustments as needed.
Dial-In Installation and O&M: With dozens, hundreds, or even thousands of PV connectors per site, there are many opportunities for installer error. Minimize risk by building detailed but replicable processes and holding installers to a high standard. For example, one common mistake is leaving connectors staged but not attached during installation, which allows debris and moisture to enter. Avoid this by capping all connectors until they can be plugged in.
Use the Right Tools: It sounds obvious, but make sure to use the right tools in the right way when installing PV connectors. Each manufacturer has specific tools and installation requirements (e.g., torquing specifications) listed in their assembly instructions. Failure to follow these instructions can result in damaged or improper connections.
Trust But Verify: QA/QC is the ultimate backstop for early issue detection. Verify connector health after shipping or other transport. Test connector circuits for electrical continuity before commissioning. Perform routine maintenance checks post-installation, including thermal imaging, to look for hot spots that may indicate an improper or damaged connection.
In conclusion, while PV connectors are essential components of PV systems, they also pose significant risks to performance and safety. The prevalence of connector issues highlights the need for industry-wide efforts to address standardization, workmanship, and quality control. By shining a light on these issues and working toward shared solutions, we can mitigate risks and ensure the long-term reliability and safety of PV systems.
Mayfield Renewables is a technical consultancy specializing in commercial and industrial PV and microgrid engineering. Contact us today for a consultation.